Contact Now : +91-9979991304 +91-7069898399
E-mail : info@omsairefractories.com / omsairefractories@gmail.com
AN ISO 9001:2015 & CE CERTIFIED COMPANY
Monolithics or Castables
Monolithics or castables
Monolithics or castables are refractory materials that have gained popularity due to their ease of installation and versatility. These materials are used in various industrial applications, such as steelmaking, cement production, and petrochemical refining. Monolithics are typically comprised of a mixture of aggregates, binders, and additives, which are then installed as a single, solid structure. On the other hand, castables are pre-formed shapes that are manufactured by pouring a mixture of refractory materials into molds and allowing them to solidify. Both monolithics and castables offer excellent thermal insulation and resistance to high temperatures, making them ideal for lining furnaces, kilns, and other high-temperature equipment. Additionally, their ability to be customized and quickly installed makes them a cost-effective solution for many industries.
Monolithics and castables are two types of refractory materials used in high-temperature applications. Here's a comparison of the two:
Monolithics
Definition: Monolithics are refractory materials that are installed in a single, solid piece, without joints or seams.
Types: Monolithics include materials like castable refractories, gunning mixes, and plastic refractories.
Installation: Monolithics are typically installed using a single-step process, such as casting or gunning.
Advantages:
Reduced installation time and labor costs
Improved thermal shock resistance
Enhanced structural integrity
Disadvantages:
Limited shape and size flexibility
May require specialized installation equipment
Castables
Definition: Castables are refractory materials that are mixed with water to form a workable paste, which is then cast into a desired shape.
Types: Castables include materials like insulating castables, dense castables, and low-cement castables.
Installation: Castables are typically installed using a casting process, where the mixed material is poured into a mold or form.
Advantages:
High flexibility in shape and size
Can be installed using a variety of methods (casting, vibration, etc.)
Often less expensive than monolithics
Disadvantages:
May require longer installation time and labor costs
Can be more prone to defects and inconsistencies
Key Differences
Installation method: Monolithics are installed in a single piece, while castables are mixed and cast into a desired shape.
Flexibility: Castables offer more flexibility in terms of shape and size, while monolithics are limited to a single, solid piece.
Cost: Castables are often less expensive than monolithics, especially for complex or custom shapes.
Choosing Between Monolithics and Castables
When deciding between monolithics and castables, consider the following factors:
Application requirements: Consider the temperature, pressure, and chemical exposure requirements of the application.
Shape and size complexity: If the desired shape is complex or custom, castables may be a better option.
Installation time and labor costs: If installation time and labor costs are a concern, monolithics may be a better option.
Budget: Castables are often less expensive than monolithics, but may require more labor and installation time.
OMSAI CRETE SUPER
OMSAI SET-50
OMSAI HEAT-K
OMSAI HEAT-C
OMSAI HEAT-A ALL REFRACTORY CEMENT
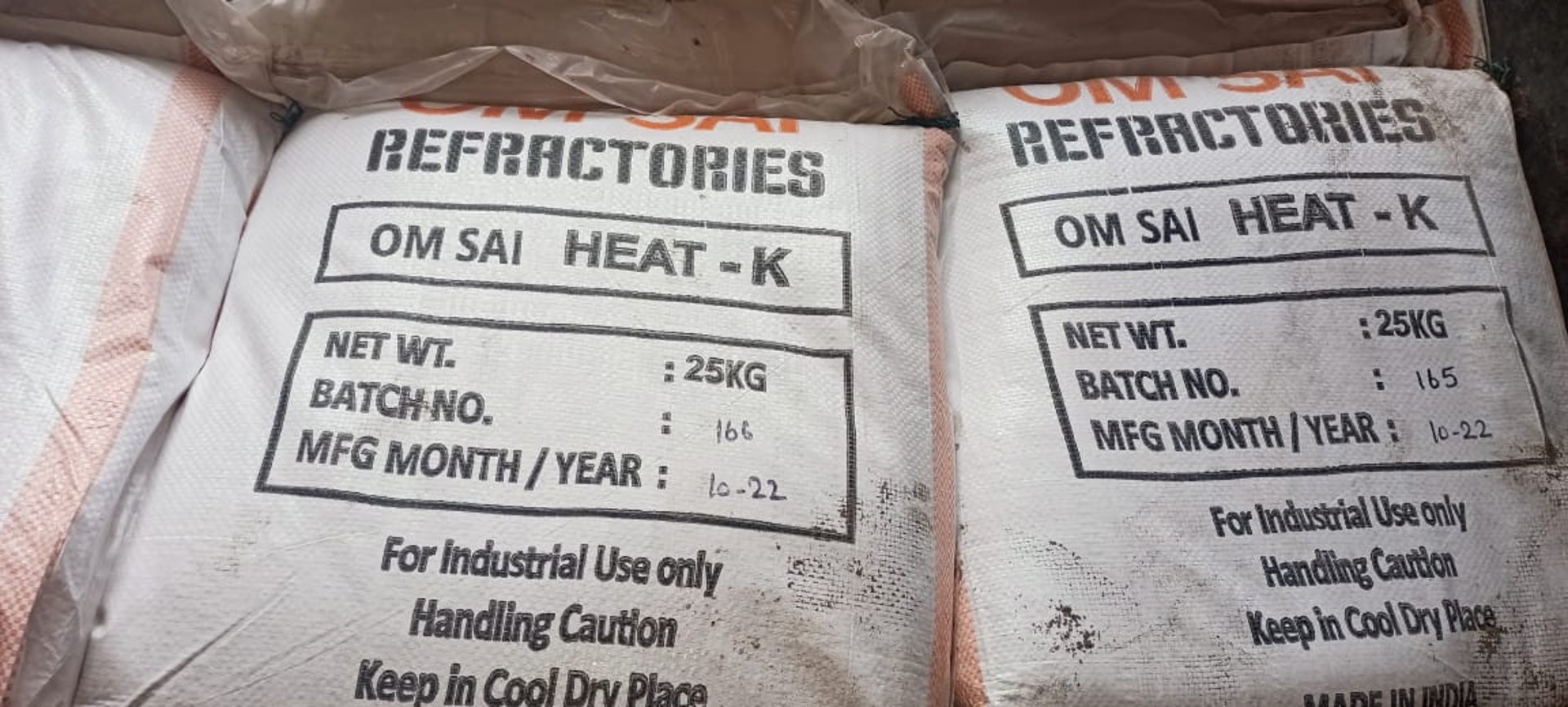
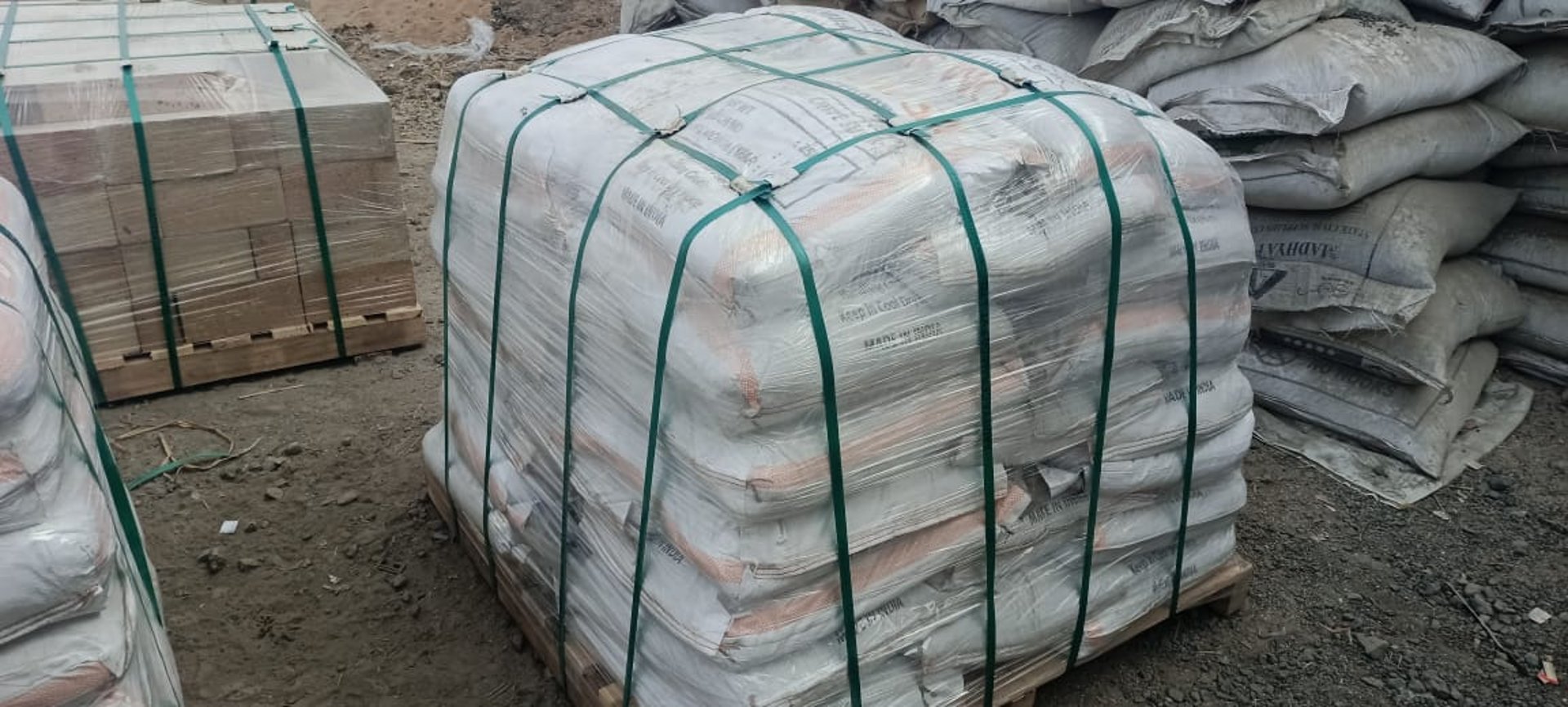
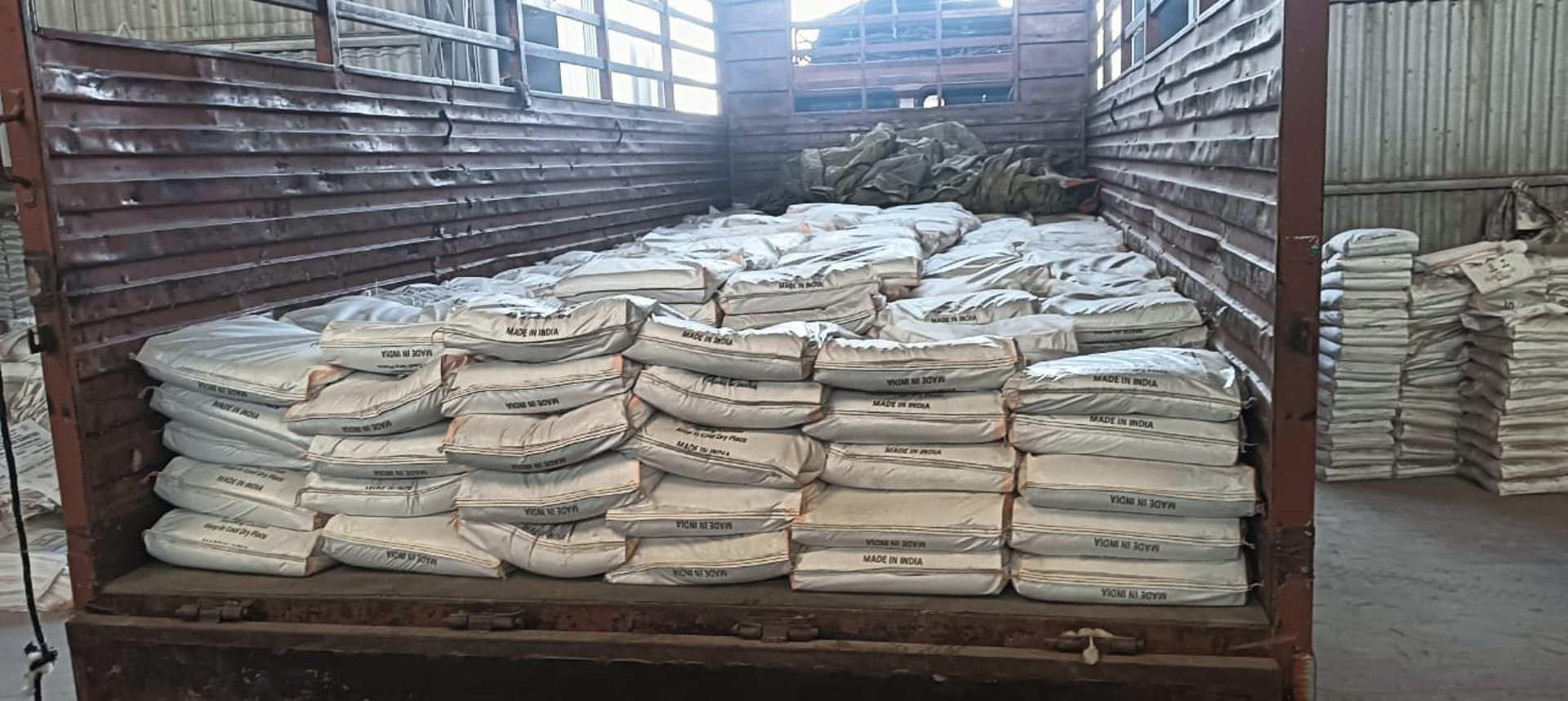
E-mail : omsairefractories@gmail.com
Contact us
(+91) 7069898399, 9979991304
Mr. Jayesh Parmar
Om Sai Refractories
Village-Chandrapur, Wankaner-363621
Dist-Morbi, Gujarat, India.
Subscribe to our newsletter
E-mail : info@omsairefractories.com