Contact Now : +91-9979991304 +91-7069898399
E-mail : info@omsairefractories.com / omsairefractories@gmail.com
AN ISO 9001:2015 & CE CERTIFIED COMPANY
Gallery
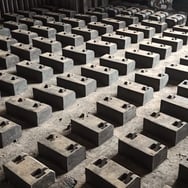
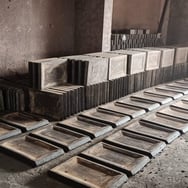
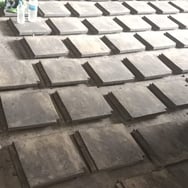
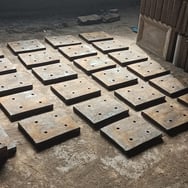
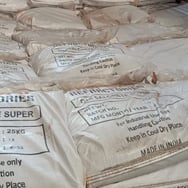
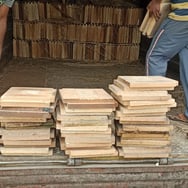
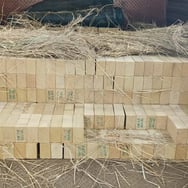
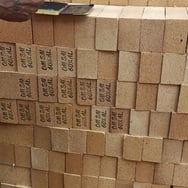
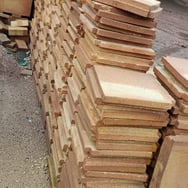
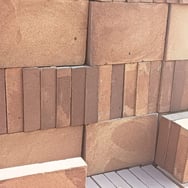
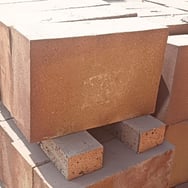
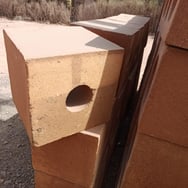
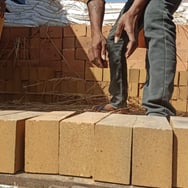
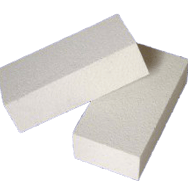
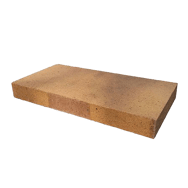
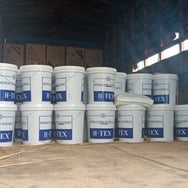

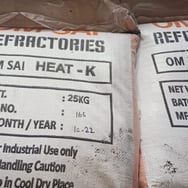
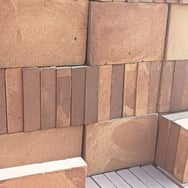
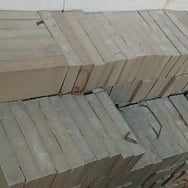
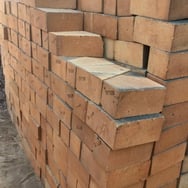
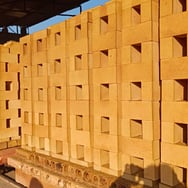
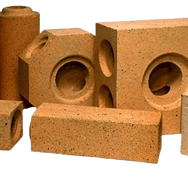
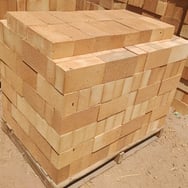
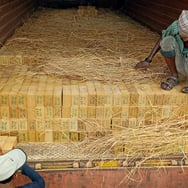
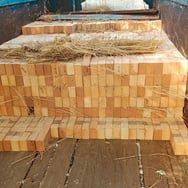
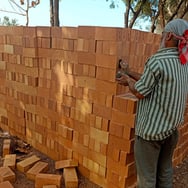
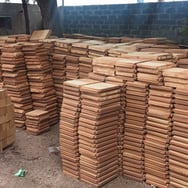
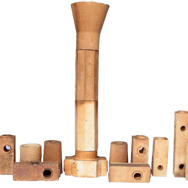
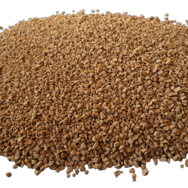
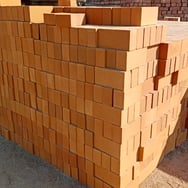
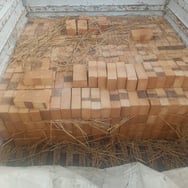

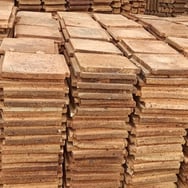
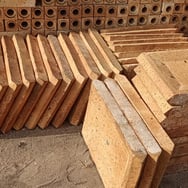
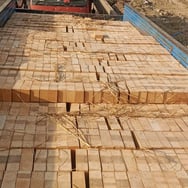
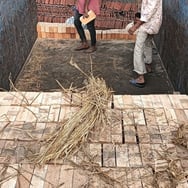
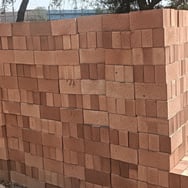
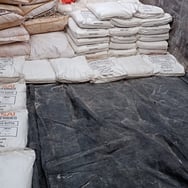
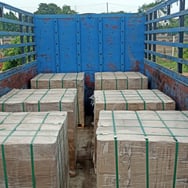
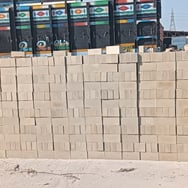
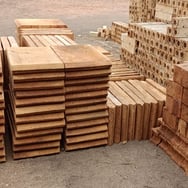
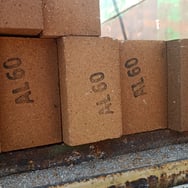
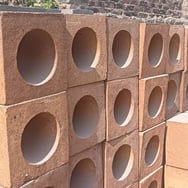
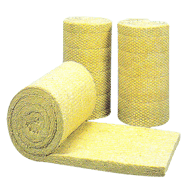
E-mail : omsairefractories@gmail.com
Contact us
(+91) 7069898399, 9979991304
Mr. Jayesh Parmar
Om Sai Refractories
Village-Chandrapur, Wankaner-363621
Dist-Morbi, Gujarat, India.
Subscribe to our newsletter
E-mail : info@omsairefractories.com